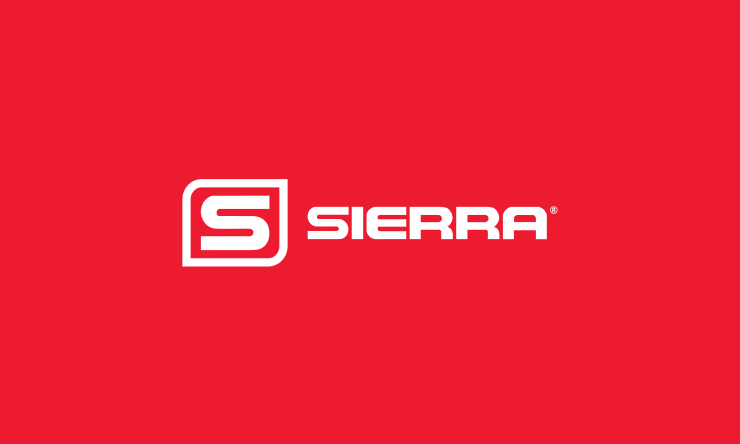
How Thermal Mass Flow Meter Technology Works
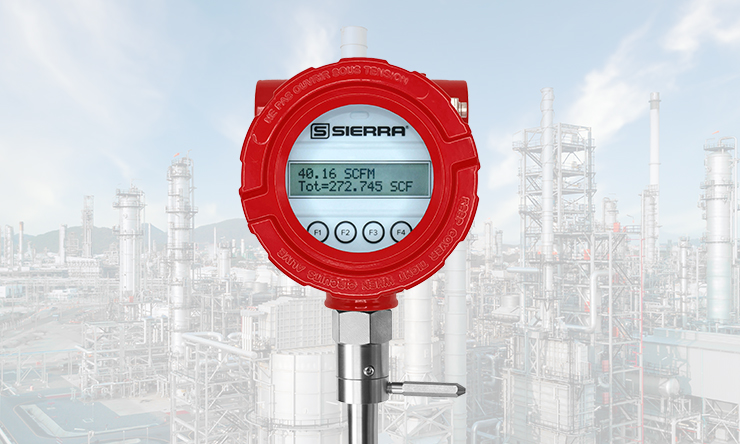
Measuring the movement of gases is critical in many industries. Inaccurate flow measurements can lead to waste, inefficiencies, loss of revenue, and safety hazards. With so many types of flow meters available, it can be challenging to select the right meter for the job.
Thermal mass flow meters offer several advantages over other types, making them a popular choice for gas flow measurement in a wide variety of industries.
Read this blog to learn more about mass flow meters and how thermal mass flow meters work.
What are Thermal Mass Flow Meters?
Thermal mass flow meters, also referred to as thermal dispersion mass flow meters or immersible thermal mass flow meters, are versatile instruments for measuring the instantaneous mass flow and total mass flow rate of gases flowing through closed conduits, such as pipes or ducts.
Unlike flow instrumentation that utilizes volumetric flow technology, thermal mass flow meters are unaffected by temperature or pressure fluctuations. They directly measure the mass flow, or actual number of gas molecules, to provide accurate flow measurement.
Basic Principles of Thermal Dispersion Technology
Thermal mass flow meters use the principles of heat transfer to determine mass flow rates. At their core, these meters have two primary sensors:
- Temperature Sensor: This element continuously measures the actual temperature of the gas flowing in the pipe regardless of flow velocity.
- Velocity Sensor (Heated Sensor): This sensor is heated continuously via electrical wattage to a constant temperature differential that is always maintained between the two sensors.
- Gas molecules act like tiny heat transporters. As they flow past the heated velocity sensor, each molecule absorbs a small amount of heat and carries it downstream.
The corresponding cooling effect is measured and compensated for instantaneously by the instrument's sensor drive electronics, which instantly add more heat to the sensor to maintain that constant temperature differential. The amount of heat required to maintain the constant temperature differential is directly proportional to the cooling effect of the gas molecules flowing by the sensor. This allows the sensor to calculate a mass flow measurement.
Watch the informative video below for a comprehensive explanation of the principles behind thermal mass flow meters
Components of Thermal Mass Flow Meters
Thermal mass flow meters encompass several essential components:
Flow Body: The physical pipe or chamber which the fluid (often gas) flows through. The flow body is often made from durable materials like stainless steel, specifically chosen to be compatible with the process gas.
Transmitter: This electronic device serves as the meter's 'brain.' It processes sensor signals, calculates mass flow, applies calibration factors, handles sensor diagnostics, and communicates data to external systems.
Flow Sensors: Typically, there are two sensors: a heated or velocity sensor that is heated to maintain the constant differential temperature and a temperature sensor that monitors the temperature of the gas flow. Sierra’s QuadraTherm design features advanced four-sensor technology with three platinum temperature sensors and one patented DrySense mass velocity sensor, allowing it to provide extreme precision with “percent of reading” accuracy, rivaling the accuracy of Coriolis technology.
Process Fluid Conduit: This refers to the pipe, duct, or channel where the gas flow is being measured. For the most accurate readings, it's essential to have sufficient lengths of straight pipe before and after the flow meter. If that is not achievable, install Sierra flow conditioning plates.
Compression Fitting: This fitting securely inserts the flow sensor into the conduit and creates a leak-tight seal to prevent process gas from escaping.
Shoulder: Supports the sensor probe, ensuring it's precisely positioned at the correct depth and location within the conduit for accurate measurement.
This article provides a more detailed look at the role of each component in a thermal mass flow meter.
Measuring Mass Flow with Thermal Mass Flow Meters
Here's a breakdown of the process:
- Heat Transfer: The velocity sensor is heated to a fixed temperature above the gas temperature.
- Cooling Effect: As gas molecules flow past the sensor, they carry some heat away, cooling the sensor.
- Heat Measurement: The electronics measure the energy needed to maintain the heated sensor at its target temperature.
- Mass Flow Calculation: The energy required to maintain the sensor temperature is directly proportional to the mass flow rate of the gas. The meter uses this information to calculate the flow rate precisely.
Applications of Thermal Mass Flow Meters
These meters are used in many industrial and research applications, including:
- Flare Gas Monitoring: Measuring emissions for compliance, the ability to accurately measure changing gas compositions
- Compressed Air Audits: Uncovering waste and optimizing efficiency
- Natural Gas Distribution: Accurate billing and process control
- Wastewater Treatment and Biogas: Aeration flow optimization and renewable natural gas
- Semiconductor Industry: Monitoring gas flows in fabrication processes
- Carbon Dioxide: Chilling food and fermenting beverages
- Nitrogen and Oxygen: Used in production plants
- Argon: Iron and steel-making
The Importance of Proper Calibration
A flow meter's accuracy depends entirely on its calibration. To ensure the best performance, thermal mass flow meters must be calibrated using a closed-loop system that simulates the exact conditions of the real-world application.
This requires using the same gas, temperature, and pressure settings that the meter will encounter in the field. Sierra prioritizes accuracy with state-of-the-art NIST-traceable closed-loop gas calibration systems.
Our meticulous approach ensures reliable flow measurements even in the most demanding applications. Be aware that some less precise calibration methods may only use air and operate at ambient conditions, impacting accuracy in real-world use.
Industries Where Thermal Mass Flow Meters Excel
Thermal mass flow meters are used in a wide range of industries, including:
- Clean energy
- Natural gas distribution
- Flare gas
- Compressed air in manufacturing facilities
- Semiconductor Manufacturing
- Wastewater treatment and biogas
- Natural gas to burners & boilers
- Carbon Dioxide for chilling food and fermenting beverages
- Nitrogen and Oxygen in production plants
- Argon for making iron and steel
To explore the many applications and industries where Sierra's flow meters are used, visit these links on our website:
Alternatives to Thermal Mass Flow Meters
Other technologies for measuring flow rates include:
Coriolis Mass Flow Meters: These meters directly measure mass flow with high accuracy but can be more complex and expensive.
Velocity Meters (Vortex, turbine, ultrasonic): These meters measure fluid velocity, which must then be converted to mass flow rate, potentially introducing additional calculations and sources of inaccuracy.
Differential Pressure Flow Meters: DP meters measure the pressure difference across a restriction in the flow path. They are a mature technology but only offer limited turndown, can be affected by changes in fluid properties, and require complicated installation and maintenance. These meters must compensate for temperature and pressure to output mass flow and can introduce additional inaccuracies.
Positive Displacement Meters: These meters directly measure volumetric flow by repeatedly isolating and moving known fluid volumes. They are accurate but can be less suitable for large flows or applications with particles. These meters also must compensate for temperature and pressure to output mass flow, and this will cause a degradation in accuracy.
Thermal mass flow meters offer several advantages over these alternatives, including:
- Direct Mass Flow Measurement: These meters directly measure mass flow, eliminating density or temperature compensations that might be needed for volumetric flow meters.
- Wide Measurement Range: Capable of measuring both low and high flow rates.
- No Moving Parts: This design reduces wear, which requires less maintenance and makes the meter more reliable
- Versatility: Suited to various gasses and pipe sizes.
- Fast Response Time: Thermal mass flow meters rapidly adapt to changes in flow conditions.
To see a helpful comparison chart that illustrates the advantages of thermal mass flow meters over the above alternatives, refer to this article.
Sierra Flow Meters
Sierra offers a range of flow measurement solutions to meet diverse application needs. In addition to our QuadraTherm 640i/780i, SteelMass 640S, and FlatTrak 780S meters, we also offer the TM500 and TM100 thermal mass flow meters. These meters utilize Sierra's robust DigiSense™ sensor technology for accurate and reliable flow measurement.
The TM500 is designed for demanding industrial applications in facilities management, chemical plants, and gas refineries. It offers exceptional accuracy and field flexibility with both inline and insertion options. It’s available with AC or DC power. The optional Gas-Mix™ feature allows users to easily switch between gases in the field.
The TM100 is ideal for burner and combustion applications, compressed gas monitoring, and leak detection. It delivers excellent value, wide measurement range, and is powered by 12-24 VDC. Like the TM500, the TM100's Gas-Mix™ feature ensures adaptability. Both meters offer fast delivery and convenient sensor validation with Sierra's TM-CAL tool.
Sierra: Your Partner in Flow Measurement
Sierra Instruments is a leader in developing and manufacturing thermal mass flow meters and other innovative flow instrumentation. We have over 50 years expertise in this field. Our goal at Sierra is to help you make your operation smarter and more productive with precision flow measurement tools we design and build to meet your application, budget, and delivery needs.