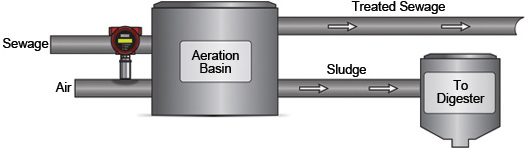
As a result of clean energy mandates and the rising cost of energy, wastewater treatment facilities around the country are retrofitting their instrumentation to run highly efficient, cost-effective, clean facilities. To reduce emissions and produce clean energy, solid wastes are often digested in large digester tanks to reduce the volume of waste (sludge) and produce more biogas, which is then used as fuel in the cogeneration process. However, a clean environment calls for not just clean air and clean energy, but clean water as well.
In the critical secondary stage of wastewater treatment, blowers aerate the basins, removing about 85% of the organic matter by making use of the bacteria living within it. Municipalities need precise mass flow measurement instrumentation to bubble the exact amount of air into these aeration basins for the bacteria to flourish.
SIERRA’S SOLUTION
In the 1980’s, many municipalities used differential pressure (dP) devices to measure the mass flow rate of air delivered to their aeration basins, but these devices proved to be expensive to maintain, clogged easily, measured only volumetric flow, and required a separate pressure and temperature transducer and flow computer to deliver true mass flow. Because of these pitfalls, municipalities began searching in the 1990’s for an alternative to these costly and inefficient dP devices.
In 2003, a large western city retrofitted their aeration basins with Sierra’s SteelMass™ 640S to precisely measure the mass flow rate of air bubbling into the aeration basins in their secondary stage of waste treatment.
By automating their aeration with the 640S as a key input into the control loop in a 7.8 million gallon/day plant, the company saved approximately $50,000 a year in aeration costs and reduced chlorination and pH adjustment costs as an added benefit. Nearly total nitrogen removal was accomplished, resulting in improved effluent suspended solids.
Sierra differentiates its thermal mass flow meters with patented Dry-Sense™ Sensor Technology. Unlike other thermal mass flow meters, Sierra’s sensors use no organic fillers or cements in device construction. With the thermal expansion and contraction that is common to thermal mass flow technology, organic or “wet” sensors crack and shift over time, changing the “skin resistance” of the thermal sensor, and thereby causing drift or outright failure.
By design, Sierra’s proprietary “dry” sensor technology is extremely accurate, stable, and holds calibration accuracy for the life of the product. Sierra has backed up those claims by being the only company to offer a lifetime warranty on its thermal sensor. Sierra’s validation software also allows the end-user to validate instrument accuracy onsite periodically. If the validation ever fails, Sierra will replace the sensors and recalibrate the instrument free of charge.
With an installed base of over 10,000 instruments in wastewater applications globally, Sierra is a proven leader in helping cities around the country measure true mass flow directly with one instrument which provides greater turndown, improved accuracy, and a lower cost-of-ownership.
Here’s what makes Sierra’s SteelMass 640S an ideal choice:- Highly accurate calibration to precisely match the application conditions
- Installed base of 10,000 instruments in wastewater applications
- Provides savings up to $50,000 a year in aeration costs
- Patented Dry-Sense™ Sensor Technology prevents sensor drift
- Field validation of accuracy and instrument health
- Lifetime sensor warranty