Official Blog of Sierra--Let's Talk Flow!
Solar…the Ultimate Killer App!
For most of us, landing an OEM for hundreds of MFCs per year is a dream account. But, imagine selling thousands or even tens of thousands of MFCs to the same customer each year. This is happening in the solar industry today and Sierra is taking a leadership role.
Making electricity from sunlight shows huge global potential and is certainly a major facet of Sierra’s Clean Energy campaign. This process is called photovoltaics, the technical term for generating electrical power by converting solar radiation into direct current electricity using semiconductors. As of 2010, solar photovoltaics generated electricity in more than 100 countries. While comprising a tiny fraction of the total global power-generating capacity from all sources, solar is the fastest growing power-generation technology in the world. In short, we’re looking at the classic opportunity to “get in on the ground floor” with Sierra products.
Conventional Solar Cells
There are really two solar cell markets…conventional and thin film. Making a solar cell the conventional way (mono-crystalline silicon cells) involves growing a silicon crystal, cutting and polishing it. Sierra’s flow controllers are an important part of the growth and polishing processes. In the most widely used crystal pulling systems, stability of the system is the most important. Since the crystal takes a long time to grow, any variation in temperature of the atmosphere inside the furnace can render the crystal unusable. In this process, the new Sierra Smart Trak® 50 Series Medium Flow controller is used to maintain a constant purge flow of Argon into the furnace. This leads to an inert atmosphere (keeping impurities out of the growing crystal), while the constant flow rate causes complete mixing and thus equalizes temperatures throughout the furnace. Sierra currently has hundreds of ST 50 Medium Flow instruments installed in this application in China (currently the world’s leading manufacturer of solar cells), with the possibility of of sales of thousands more.
The ST 50 Medium Flow is ideal for relatively high flows of two gases (Argon or Nitrogen is typically used) that do not require high accuracy, but very high repeatability. Units must be economical and simple to control. Above all, they must be stable and reliable.
Polishing Processes
Once the crystal has been grown, it must be cut into slices for the cell and then polished. One polishing process uses frozen Argon particles in an Argon carrier gas to “blast” any imperfections from the surface of the crystal. The Side-Trak® 840H High Flow is used to control the carrier gas flow rate. This application was discussed in detail in the previous issue of this newsletter. Sierra supplies hundreds of these 840H controllers to FSI, the leading manufacturer of these polishing machines.
FSI Antares® Cryokinetic Cleaning System
Thin-Film Solar Cells
A second way to make solar cells is using thin films. These have material costs that are trending lower (though still not as cheap as the above), but the initial tooling is more expensive. They are also not as efficient as mono-crystalline cells, so you must make more of them. This technology is most common in Europe and is still developing.
Many different photovoltaic materials are deposited with various deposition methods (PVD, sputtering, CVD…all common applications for Sierra) on a variety of substrates. Thin-film solar cells are categorized according to the photovoltaic material used:
Amorphous silicon (a-Si) and other thin-film silicon (TF-Si)
Cadmium Telluride (CdTe)
Copper indium gallium selenide (CIS or CIGS)
Dye-sensitized solar cell (DSC) and other organic solar cells.
Sputtering is a form of Physical Vapor Deposition. Smart-Trak controls the sputtering gas flow rate. Obviously, those specialized gases require flow controllers with compatible wetted materials. The Smart-Trak® 2 – 100 Series is perfect for this application. Precise control of the carrier gases for the various semiconductor doping compounds is critical, as is control over purging the chamber of these gases between deposition steps. These units require high accuracy and linearity. Digital communications are required to network these controllers into complex semiconductor tools. Finally, since much research is still being conducted to optimize the recipes to manufacture these various thin films, Dial-a Gas® is a useful option as well.

Scott Rouse, Product Line Director
Sierra Instruments
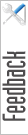