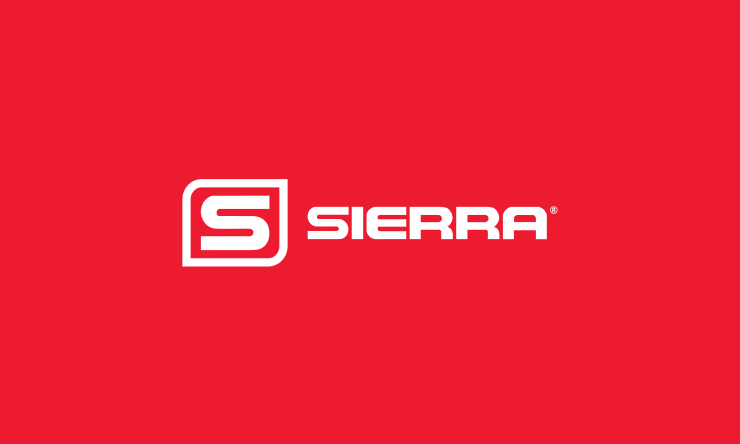
Best Practices for Mass Flow Controller Selection & Installation
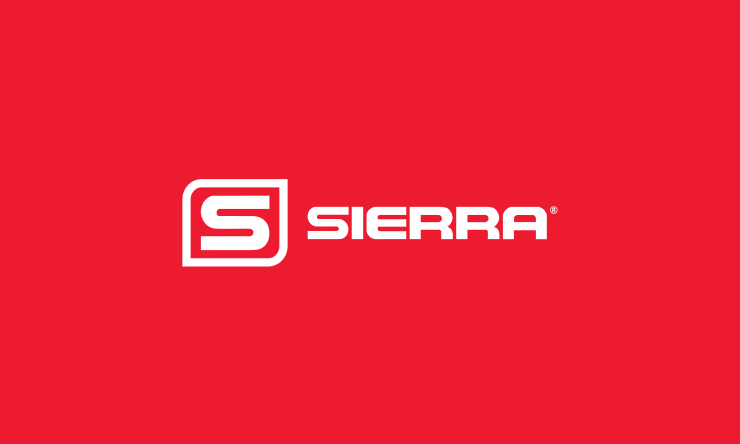
As scientists, facilities managers and manufacturing engineers, specifying equipment is a part of our daily work life. What product do I need? What's the best price for the value? How do I install the product once I get it? The more information about best practice principles, the easier the job is of specifying and buying equipment. Through our years of experience of specifying, installing, and servicing mass flow controllers, we have compiled a comprehensive list of best practices by users for the selection, safety, installation, and operation of their thermal mass flow meters and controllers are as follows:
Best Practices-Product Selection
1. Select only those mass flow meters and flow controllers where the manufacturer’s specifications meet the conditions of the application, such as maximum and minimum flow rate, pressure and temperature. Some manufacturers have software programs that recommend the instrument model best suited for your application.
2. To minimize pressure drop and flow non-uniformities, you should select the instrument with the largest inlet fittings compatible with the size of the process line. In the case of corrosive gases, the instrument selected should have materials of construction that provide protection against corrosion.
3. Size the instrument so it operates in the upper two-thirds of its full scale mass flow rate range.
Installation and Set-Up
4. Install the instrument only in process lines that meet the manufacture’s pressure and temperature ratings. A margin of safety should be provided if spikes and surges exist in the process. Proper pressure relief valves and burst plates should be installed in high pressure applications.
5. To avoid obstructions in the sensor tube and the narrow flow channels in the laminar flow element, you should install the instrument in process lines that have clean gases. Upstream particulate filters properly sized for the flow rate, with a minimum rating of 5 microns are recommended for all applications.
6. To avoid thermal siphoning (or, the so-called, “chimney effect”), you should install the instrument in the process line with the axis of the flow body oriented horizontally, not vertically. At zero flow, if the axis is vertical, the gas heated by the sensor tube rises upward through the sensor tube and creates a closed flow loop in the flow body that causes the instrument to read a flow rate when there is none. This effect is significant only in the very lowest portion of the full scale range. If system constraints require vertical mounting, then the instrument should be re-zeroed in the field. Vertical mounting requirements should be communicated to the manufacturer upon order so the instrument can be adjusted to meet these special requirements.
7. To avoid stress on the springs in the control valve, particularly in medium- and high-flow mass flow controllers, you should install the instrument in the process line with the axis of the flow body oriented horizontally as required above and, additionally, with the control valve located on top of the flow body, not on the bottom or the side. If system constraints require a different instrument orientation, you should communicate this requirement to the manufacturer upon order so that adjustments can be made.
8. After turning on the instrument, you should allow the instrument to warm up for the time period specified by the manufacturer. A warm-up time of about 10 to 30 minutes typically is required for the instrument to reach full accuracy.
9. Be sure to zero your mass flow meters and controllers prior to first use and periodically afterward on a schedule based on the manufacturer’s recommendations or your own experience. The zero flow output signal should be averaged over a sufficient time interval. Preferably, zeroing should be performed with the actual gas to be measured at the same pressure and temperature of the application, or close to it. If there is a change of gas, the instrument should be flushed with the new gas before being zeroed. Obviously, for proper zeroing, the flow rate must be zero. This is best accomplished, in the case of controllers, by commanding the control valve to be shut, and, in the case of both mass flow meters and controllers, by closing shut-off valves installed just upstream and downstream of the instrument. In the absence of these valves, the process line must have other means to insure that the flow is zero.
Following these best practices are sure to result in the most accurate measurement outcome with your new mass flow meter or controller. Have any other tips we didn’t mention or questions about mass flow control? Please leave them in the comments section below.