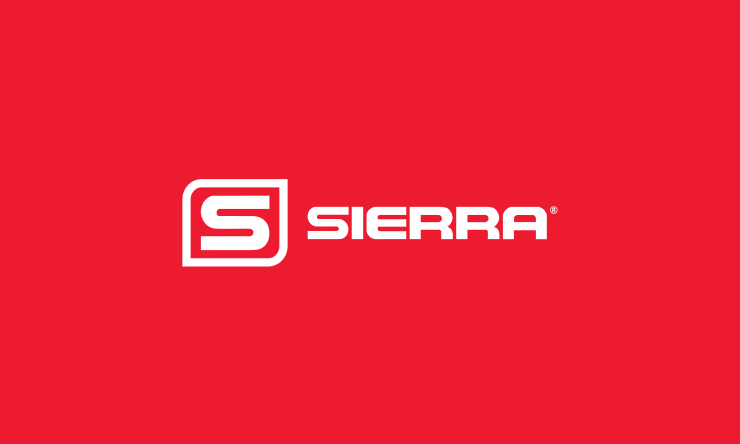
DrySense Sensor Technology Is the Key to Thermal Flow Meter Accuracy
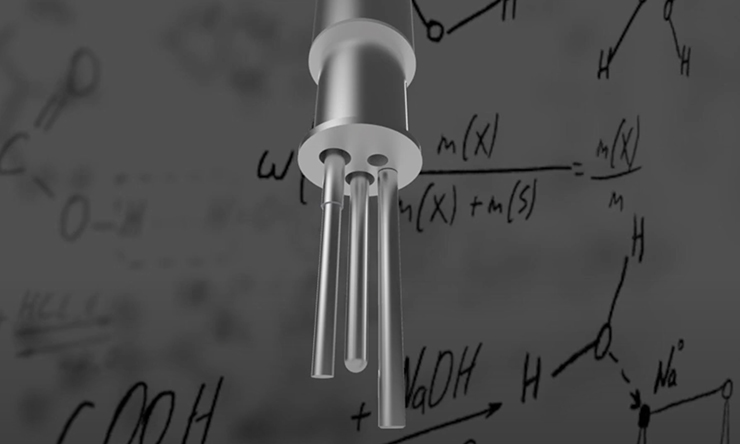
Why Are Dry Sensors Critical for Flowmeter Lifetime Sensor Warranty, Accuracy, and In-Situ Validation?
When it comes to flow meters, what matters to plant managers and engineers alike is if their meter is measuring flow accurately and reliably. They want to know they can depend on the data their meter is providing. However, the answer to this question really depends on the type of sensor design of the thermal mass flow meter. For this reason, designing a stable sensor that will last over the lifetime of your thermal mass flow meter is the holy grail in thermal mass flow meter design. However, the truth is most flow meter manufacturers use a “wet’ sensor design.
Wet Sensor Design
Why is a wet sensor problematic? As conditions in your application change, the sensor is heated and cooled over time, expanding and contracting the cement inside the sensor—and you know what happens to cement as it is repeatedly heated and then cooled, it shifts and cracks. This “wet” sensor design greatly compromises the accuracy of the thermal sensor over time. Since thermal sensors are precisely calibrated to determine the heat transfer versus flow characteristics, any change in the physical makeup of the sensor layers will invalidate this calibration, resulting in drift or outright failure. Excessive drift means users must send the meter back to the factory for recalibration.
DrySense Sensor Differentiator, No-Drift Stability
To minimize the drift in a thermal sensor the epoxies, cements and thermal greases that make up the wet sensor need to be removed. Addressing this very need, Sierra introduced a patented dry sensor in 1999.
Patented Dry Sensor Technology
The patented no-drift DrySense velocity sensor technology uses a proprietary swaging process which eliminates all air gaps between the heated velocity sensor and the tubular probe sheath eliminating the need for any potting compounds. The result is maximum sensitivity, reproducibility, immunity to cracking and shifting over time, and ultimately greatly improved accuracy, all backed by a lifetime warranty.
All materials used to make the sensor are selected to assure that the coefficients of thermal expansion are approximately the same. As a result, they expand and contract at the same rate, limiting the stress and cracking. Sierra determined that using a dry sensor was the only way a manufacturer could claim stability over the sensor’s lifetime.
Dry, no-drift sensors make accurate in-situ calibration validation possible. The all-metal, epoxy-free mechanical design provides the confidence that the in-situ calibration validation is actually valid. If the sensor innately drifts, in-situ calibration will inherently be inaccurate.
How DrySense Technology Works
Discover more about DrySense technology, by downloading the In-Situ Calibration white paper.
Editor’s Note: This post was originally published on March 1, 2015. Due to its popularity and continued questions on this issue, we updated the post on February 18, 2021.