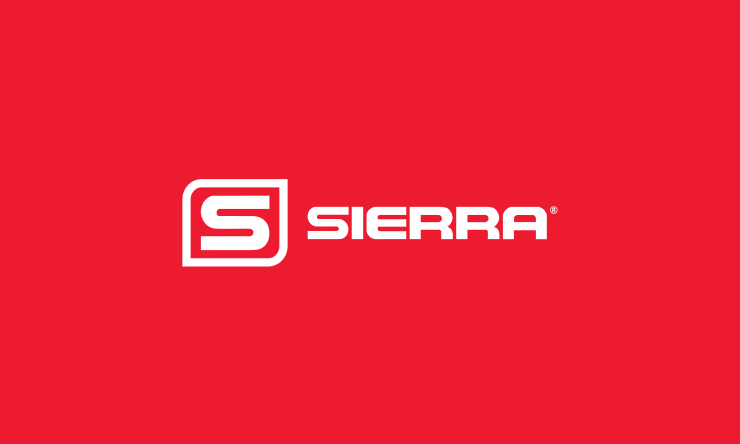
Methods & Pitfalls of In-Situ Calibration Validation of Thermal Flowmeters
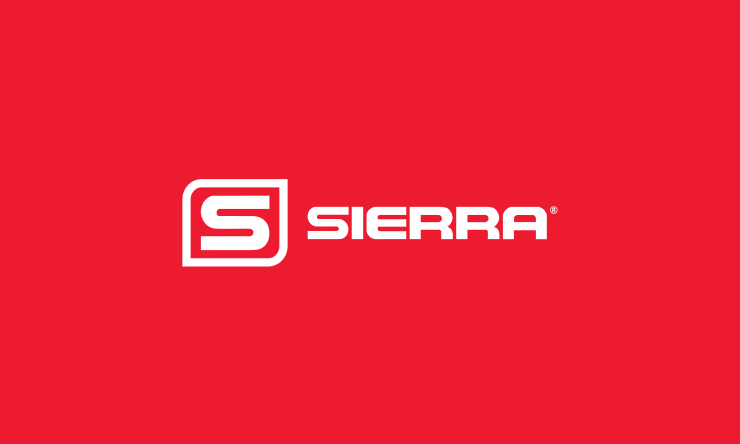
Driven by the need to meet quality standards like ISO 9001, reliability engineers for mid-to-large-sized facilities and campuses know the time consuming reality of assuring their flow meters are properly maintained and "in cal". A unique and highly marketed benefit of Thermal Mass Flow Meter technology is "in-situ" or "in place" flow meter calibration. This certainly sounds like an alluring proposition to save time and money by avoiding the expense of returning the instrument to the factory for annual recalibration and recertification. But, not all methods of in-situ calibration validation are created equal.
I explore five of those methods in my white paper, “In-Situ Calibration: Methods & Pitfalls of Thermal Mass Flow Meter Sensor Field Validation,” as well as the how thermal flow meter sensor design determines the validity of in-situ calibration.
When assessing your flow instrumentation, it's critical to evaluate the methods of in-situ calibration to get reliable results and avoid false positives. Your time is valuable; read on to find out more about each calibration validation method.
1. Validation Using Resistance
This simple method measures the resistance across the velocity sensor. Since the velocity sensor is most often a platinum resistance temperature detector, the measured resistance is directly related to the temperature of the sensor. This temperature should be equal to the space surrounding the velocity sensor once everything has come to equilibrium. This method only measures the resistance of the platinum wire that is wrapped around the platinum mandrel. This method does nothing to measure drift since the test doesn’t measure factors related to heat transfer from the wire through the organic epoxy fillers and sheath out into the flowing gas.
2. Validation Using Zero Flow
Zero flow is the only truly reproducible point between factory calibration and the site where the thermal mass flow meter is being used. For these reasons, many manufacturers provide data for checking zero at another set of more reproducible conditions: zero flow at atmospheric pressure and temperature. This requires the meter to be completely removed from the process and allowed to come to equilibrium at ambient conditions. At best, this stretches the definition of in-situ verification, as it is not “in place”.
3. Field Adjustments Using K-Factors
As an interim step, many manufactures enable the application of a global k-factor that works as a multiplier to the observed flow value. This is simply a linear offset most often employed to make the meter reading agree with another device. The problem with k-factors is that the inherent response curve of a thermal sensor to flow is non-linear and is best represented by a complex polynomial function, typically at least to the fifth order.
In other cases, the manufacturer may allow several points on the calibration curve to be adjusted. This is typically done for large ducts and pipes as part of a flow transit. This is sometimes erroneously called an in-situ calibration.
4. Validation Using Full-Flow
One complex and expensive technique that validates beyond a zero flow condition checks the full-flow range by generating a series of known flow rates, from zero to full scale. The system uses a small sonic nozzle opening that directs a known flow past the velocity sensor. The diameter of the nozzle is fixed, and by applying a known differential pressure across the nozzle, the flow through the nozzle can be calculated. This type of validation depends on the nozzle not becoming plugged or dirty, and it requires precision pressure gages—which themselves need periodic recalibration.
5. Validation Using Actual Flow Audit Method
Perhaps the best in-situ calibration method, the Flow-Audit Method, uses a high-accuracy flow standard to prove the accuracy of the flow device under test. The ideal meter for the flow audit method has the application flexibility to work on different gases and pipe sizes. Sierra’s QuadraTherm 640i insertion thermal mass flow meter is one such instrument that can be used across multiple pipe sizes and gases. It also features a patented no-drift, dry sensor that results in a stable, reliable measurements.
For more on calibration validation, check out a recent post from Product Line Director Scott Rouse, The Truth About In-Situ Calibration Validation of Thermal Flowmeters. And be sure to download my whitepaper, "In-Situ Calibration: Methods & Pitfalls of Thermal Mass Flow Meter Sensor Field Validation," for more in-depth information.