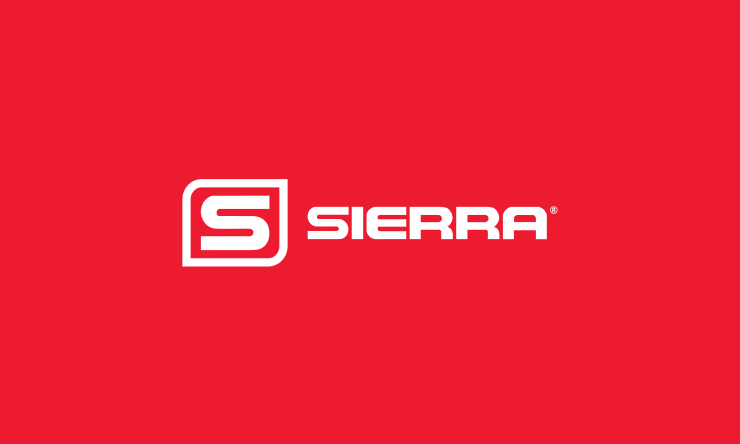
Flow Energy Management: 3 Killer Apps To Lower Energy Costs
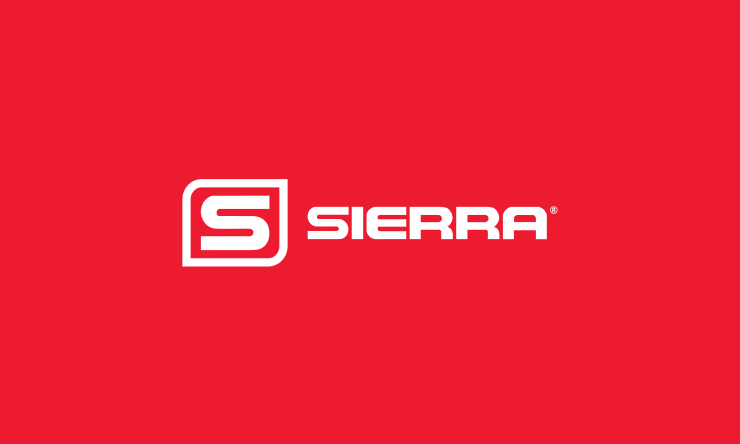
More and more, buzz words like “flow energy” or “flow energy management” have become prevalent as companies grapple to control costs, reduce energy use, and comply with government regulations---all while trying to increase profitability. But what are flow energy and flow energy management? Why should you care? In this three-part series, we will:
- Explore what flow energy is
- Discuss the applications and flow meters that really impact the bottom line
- Give tips and tricks for using flow meters to improve energy efficiency
- Look at real-world examples of managing flow energy and how they have benefited from this practice
3 Killer Apps to Lower Energy Costs With Efficient Flow Energy Management
Flow energy is defined as flows that are critical to your facility's every day operation. In other words, continuous flows that cost money. These flows include natural gas, compressed air, water, and steam.
Facilities managers often have the challenging task of managing all the flow energy in their facility. Since none of these commodities are “free,” they must strive to measure their “energy” usage accurately, determine the processes that use the most energy, and make them more efficient. These initiatives contribute directly to the bottom line.
The challenge is deciding which flow meter technology should be used for each fluid. In this first part of our blog series, we look at the best measurement applications (or “killer apps”) for optimal flow energy management for gas, liquid, and steam measurement and explore the best flow meter technology for each.
Killer App #1: Natural Gas And Compressed Air Measurement
Natural gas and compressed air measurement hit the top of the list for “killer apps” that almost every facility must measure and manage. Many facilities use natural gas for burner control in manufacturing or to fire boilers to produce steam or hot water. Facilities may require tracking of gas distribution, allocation, and billing. [caption id="attachment_6807" align="aligncenter" width="500"]
All images courtesy of Sierra Instruments
Regardless of the application, facilities managers must have precise natural gas measurements to efficiently manage flow energy and thus lower energy costs.
Compressed air is another expensive flow energy, requiring energy-intensive compressors to produce it. Facilities managers are often tasked with conducting compressed air usage audits to determine compressor efficiency, find leaks in the system, and balance distribution and allocation.
In the past, facilities have used insertion turbine meters for compressed air measurement, but turbine meters don’t work well with low compressed air flows. Alternatively, insertion pitot tubes could be an option, but they don’t measure direct mass flow. Both technologies are prone to clogging.
The mass flow advantage
Thermal mass flow meters are ideal for natural gas combustion and allocation applications because mass flow rate, not volumetric, is the quantity of direct interest. For example, the optimal fuel/air ratio for efficient combustion is calculated on a mass basis. Natural gas is also billed on a mass basis.
Measuring compressed air presents its own challenges. In many facilities, usage varies widely throughout the day from very heavy at times of peak manufacturing to small flows (perhaps due to leakage) when most production is on standby. Thermal flow meters have a very wide turndown (100:1) to handle these fluctuations. Further, they have little to no pressure drop. The facility has already paid to have the air compressed, so needless pressure drop is wasted money.
Because thermal mass flow meters count the molecules of gas, they are immune to changes in inlet temperature and pressure. In a thermal flow meter’s simplest working configuration, fluid flows past a heated thermal sensor and a temperature sensor. As the molecules of the fluid flow pass the heated thermal sensor, heat is lost to the flowing fluid. The thermal sensor cools down, while the temperature sensor continues to measures the relatively constant temperature of the flowing fluid.
The amount of heat lost depends on the thermal properties of the fluid and the flow rate of the fluid. Thus, by measuring the temperature difference between the thermal and temperature sensors, the flow rate can be determined (Figure 1).
New developments in four-sensor thermal technology, coupled with stable "dry sense" sensor technology and advanced thermodynamic modeling algorithms, enable some thermal flow meters to attain +/-0.5 percent of reading accuracy, rivaling the accuracy of Coriolis flow meters at a fraction of the cost (Figure 2). On board, software apps also enable gas mixing capability, in-situ validation, and dial-a-pipe.
Advantages of thermal mass flow meters for gases:
- Direct mass flow measurement of gases eliminates the need for temperature or pressure compensation
- Accuracy +/- 0.5 percent reading; high flows 60,000 sfpm (0-305 smps); 100:1 turndown
- Multivariable: Mass flow rate, temperature & pressure
- Advanced four-sensor "dry sense" technology minimizes drift and enables field validation
- Insertion version with hot tap capability for easy installation
- Software applications for easy set-up, in-situ calibration, dial-a-pipe, and gas mixing
- Digital communications suite
Killer App #2: Steam Production, Distribution, & Allocation
Steam is used almost everywhere in industry, from process flows in chemical plants and refineries to geothermal steam in energy production. The steam produced by a boiler must be measured in order to optimize boiler efficiency. Steam is used to heat buildings, in food processing, and in heating water. Even nuclear power plants use the steam produced from the heat of the nuclear fission.
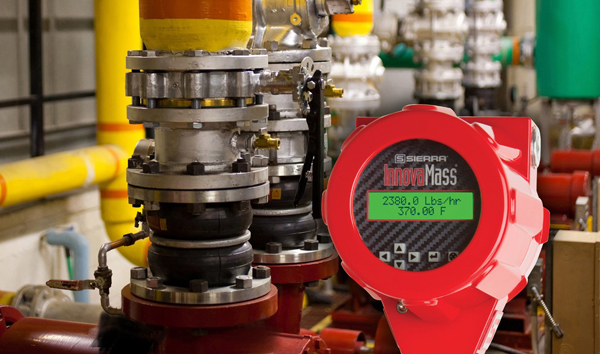
Figure 3. Multivariable insertion vortex flow meters are ideal for saturated and supersaturated steam measurement.
Traditionally, steam flow has been measured with a differential pressure device. This is typically an orifice plate. However, such devices are inherently volumetric flow measurements. Changes in pressure and temperature will change the mass flow rate of steam. Even a “small” change of 10 percent in steam pressure will result in a 10 percent error in non-compensated mass flow. This means that, in a typical differential pressure measurement installation, the volumetric flow rate measured by the device must be compensated by measuring temperature and pressure, and then these three measurements (ΔP, T and P) integrated with a flow computer to calculate mass flow.
Multivariable vortex flow meters increase accuracy
Insertion multivariable vortex flow meters allow one instrument and one process connection to simultaneously measure mass flow rate, temperature, pressure, volumetric flow rate, and fluid density (Figure 3). The density of saturated steam varies with either temperature or pressure, while superheated steam varies with temperature and pressure, so multivariable vortex flow meters assure the flow meter’s density calculations are correct. Therefore, mass steam flow measurement is correct maximizing your steam productivity.
Multivariable vortex flow meters provide steam accuracy of 1 percent of reading, 30:1 turndown plus pressure and temperature compensation.
For decades, vortex technology has been a stable and proven measurement technology for gas, liquid, and steam applications. Vortices are forces of nature, “swirls” formed as a fluid moves past an obstruction, like water flowing around a rock in a stream or the wind past a flagpole. In a vortex meter, a sensor tab flexes from side to side as each vortex flows past, producing a frequency output that is directly proportional to the flow rate (Figure 4). Multivariable mass flow is achieved when a temperature sensor is immersed in the flow stream to measure the temperature of the flowing gas, liquid or steam, while a pressure sensing port leads up to a pressure transducer. Advanced onboard software apps allow for easy set-up, meter tuning, and validation for ease of use.
Advantages of multivariable vortex flow meters for steam measurement:
- Multivariable: mass flow rate, volumetric flow rate, density, pressure, temperature
- Accuracy of up to 0.7 percent of reading; 30:1 turndown
- Dynamic density calculation improves steam metering accuracy
- Hot-tap probe retractor for easy steam installation
- Onboard software Apps like meter set up, in-situ calibration/validation, tuning
Killer App #3: Water & BTU Measurement
Water is also an expensive flow energy and limited resource. Many facilities measure water flows to verify billing, determine leakage rates, and measure influent and effluent flow. Another growing application is thermal flow energy measurement. Facilities must spend money to produce hot and chilled water for process uses or HVAC. This thermal energy must be measured for distribution, allocation, and billing.
There are of course many ways to measure water flow. Turbine or propeller meters are common but have moving parts that are prone to clogging. Vortex meters are also widely used but stop working at low flows. Magnetic flow meters are in use worldwide but cannot measure the de-ionized water that can be found in some process industries.
Clamp-On Ultrasonic Liquid Flow Meters Offer Ease of Use & Flexibility
Clamp-on ultrasonic flow meters are ideal for water flow applications. They achieve high accuracy at low and high flows, save time with no pipe cutting or process shutdown, and are not affected by external noise. Coupled with temperature sensors on the “hot” and “cold” legs, the thermal energy gained or lost can be measured (Figure 5). This has widespread usage in distributed and district energy, where central heating and cooling plants provide HVAC to the entire facility.
Figure 5. Clamp-on ultrasonic liquid flow meter with thermal energy/BTU capability
In a transit-time ultrasonic liquid flow meter, an ultrasonic signal is transmitted in the direction of the flowing fluid downstream, and then another signal is transmitted against the flowing fluid upstream (Figure 6). In its most basic form, the time for the sonic pulse to travel downstream is compared to the time for the pulse to travel upstream. This differential time is then used to calculate the velocity of the flowing fluid. The meter then uses this fluid velocity to calculate the volumetric flow rate in the pipe. BTU energy measurement can be derived from the volumetric flow rate and the temperature difference between the hot and cold legs. New developments in ultrasonic technology coupled with modern software applications allow for real-time liquid density compensation for improved accuracy and setup functions with a visual signal for a correct installation.
Advantages of ultrasonic flow meters for water/BTU measurement:
- Clamp-on or insertion transducers measure bi-directional flow
- One meter for a wide range of pipe sizes from 2 to 236 inches (5.0cm to 6.0M)
- Accuracy +/- 0.5 percent of reading from 0.16 to 40 ft/s (0.05 to 12 m/s)
- Clamp-on or insertion PT 100 temperature inputs for thermal energy/BTU measurement
- Software apps for easy set up for optimal signal strength
Putting it all together — Complete flow energy management solution
Most facilities managers must find the right flow meters to measure at least one and often all three of these “killer apps” to successfully manage the flow energy in their facility. Determining the best flow meter technology for the flow energy management of gas, liquid, and steam applications depends on specific measurement goals, fluid, flow rate, turndown requirements, temperature, and pressure. To outfit a facility, it’s essential to work with a proven flow measurement company with a team of experts in each flow meter technology.
The best case scenario is to deal with one flow meter company to specify and support instrumentation for all your gas, liquid, and steam flow measurements. This would mean one point-of-contact for product specification and installation, one operating system for easy integration, and one local support team over the lifetime of the product.
Advantages of one complete flow energy solution:
- One company and point-of-contact for product specification for all gas, liquid, and steam flow meters
- One commissioning team for all three technologies
- Specialized, local support team for all three technologies
- Shared software applications and operating system for easy integration
- Localized calibration expertise and assets to ensure accuracy over the lifetime of the product
Next week in part 2, we will look at flow energy devices and discuss installation tips & tricks for three common energy flow measurement solutions. Proper flow meter installation is key to ensuring optimum performance of the instrument within the application. Next week's blog considers tips and tricks to overcome common flow measurement challenges.
Want information on Sierra's one complete flow energy solution? Click here.