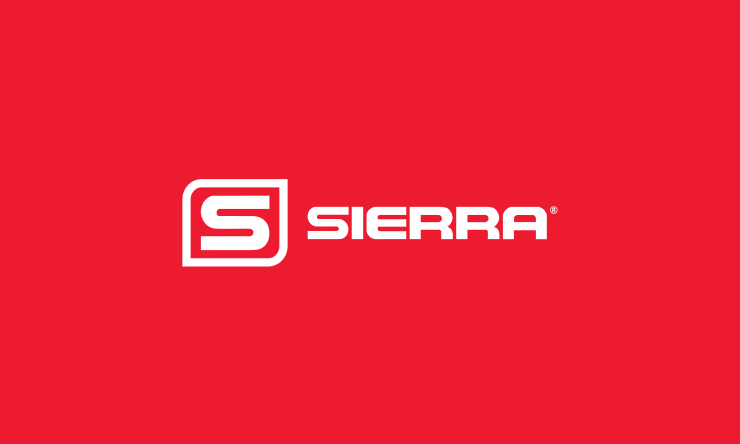
How to Attain Precise CO2 Injection in the Carbonated Beverage Production Process
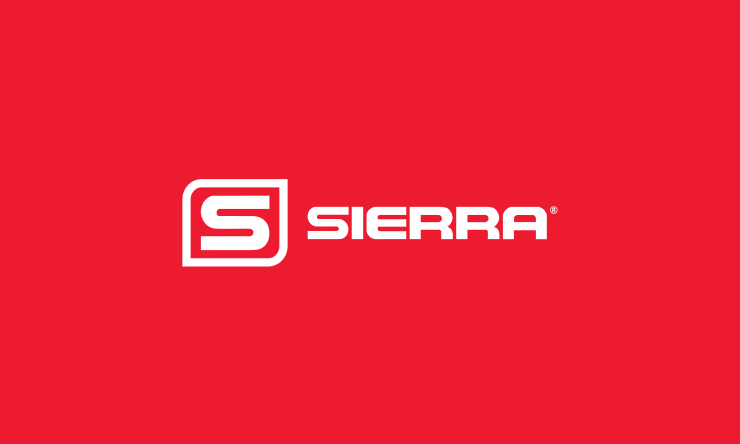
Looking for the perfectly carbonated beverage? Is your CO2 injection process leaving your drinks flat? Industrial mass flow controllers offer the perfect solution for controlling the exact CO2 injection into beverages to create the perfect foam for the beer industry or carbonation for popular soft drinks.
It is pivotal that carbonated beverage manufacturers have the ability control the exact amount of carbon dioxide (CO2) being injected into their beverages during the bottling process. Mass flow controllers (MFCs) are used to regulate and control the amount of CO2 injected into the bottles during filling and capping to assure uniformity of the product (see diagram below).
The beverage bottling process.[/caption] Too much CO2 in the beverage will result in an overly carbonated beverage, and could possibly break bottles causing a plant safety issue and loss of product. While an inadequate CO2 injection will cause the beverage to be “flat.” In either situation, the batch would need to be tossed out resulting in a loss of product which costs the company countless dollars in revenue and ultimately hurts profit margins.
Many companies use volumetric flow and differential pressure devices for gas flow control for their CO2 injection in the carbonated beverage production process. However, volumetric flowmeters are not suitable for this application because of the widely varying mass flow requirements encountered in start-up and low production periods.
Direct mass flow control with thermal mass flow controllers like the MaxTrak 180 industrial flow controller, part of the SmartTrak family, provides smooth, stable, accurate, and repeatable CO2 gas mass flow control you can rely on, every time. In essence, counting and controlling every gas molecule flowing through the instrument to achieve unmatched precision. Unaffected by upstream gas temperature and pressure fluctuations, gas mass flow control is direct and unequivocal.
MaxTrak meets industrial MFC requirements with NEMA 6 & IP7 ratings and provides the robust, smooth mass flow control required for the brew and beverage process industry.
Learn how SmartTrak mass flow controllers are ideal for OEM/systems integrator mass flow applications.