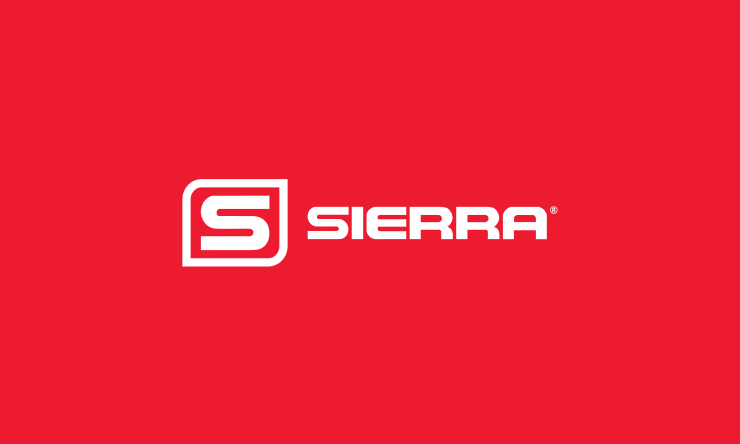
Part 1: Accurately Measuring Flare Gas -- Challenges, Solutions, and Opportunities
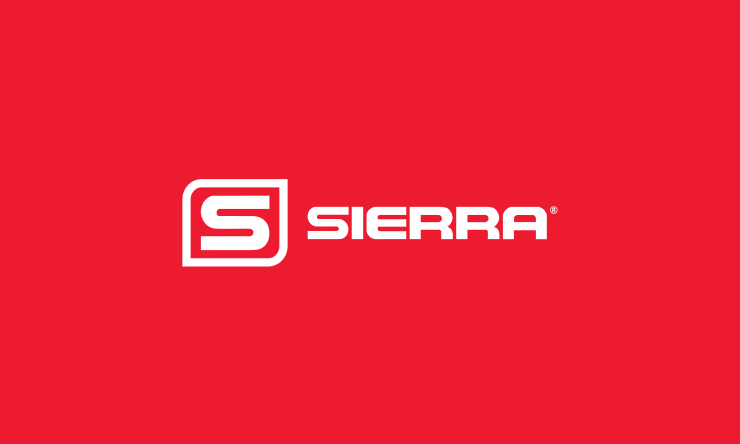
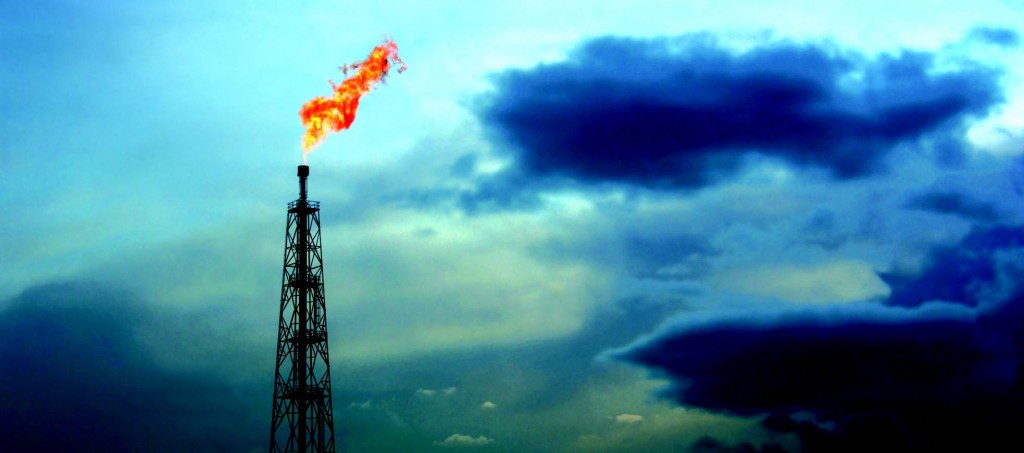
- Wide Flow Rate Variations. Turndowns of up to 1,000:1 may be required.
- Non-Uniform Flow Profile. Flare stacks generally have asymmetric and swirling flow.
- Very Low Pressure with Variable Temperatures. Most flare headers operate at near atmospheric conditions. Gas temperature varies with well depth and reservoir characteristics.
- Dirty Flares Versus Clean Flares. Many flares have significant amounts of dirt, hydrogen sulfide, wax, tar, and other paraffins that make for a dirty, sooty flame.
- Maintenance Is Difficult and Costly. Roaring flames, difficult access and regulatory requirements make flares difficult to service.
- Wide Gas Density Variations. Flare gas composition, and thus the density of flare gas varies over the lifetime of the flare. Traditional flow meters cannot successfully manage the changes in flare gas composition.