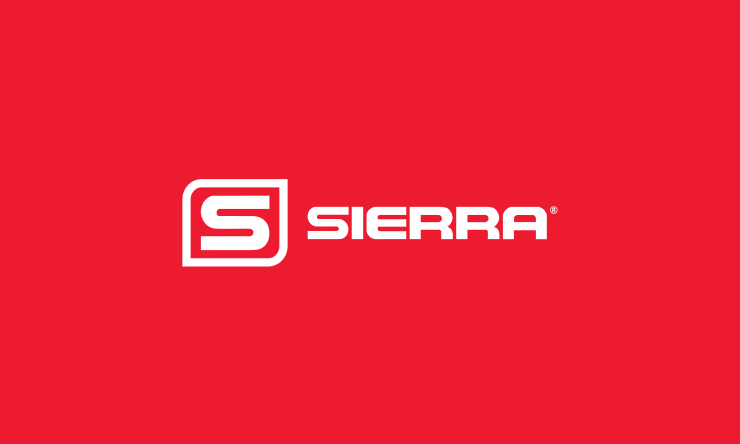
Part 3: Accurately Measuring Flare Gas -- Managing Gas Mix Changes, Retaining Accuracy, Reducing Cost of Ownership
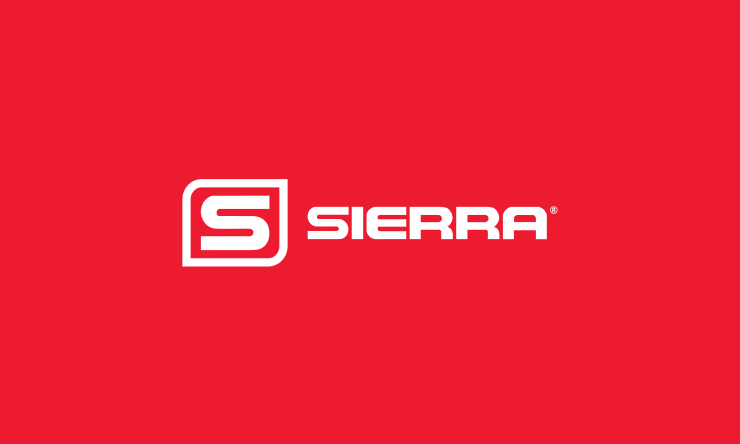
Flow Meter Flexibility and Accuracy
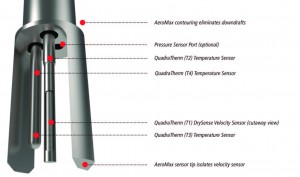
Avoid Costly Recalibration
In thermal mass flow meters, the gas mixture composition of the gas is required at time of purchase. Flare composition sampling depends on the wellhead and is typically done once every three months. Once the flare gas composition is known, operators can create, name, store and upload new proprietary gas compositions to the meter (see Figure 1). Accuracy is maintained without you having to send the meter back to the factory for costly recalibration. The meter itself stores four gas compositions. Operators can access the software’s gas library, which is password protected to keep proprietary gas mixtures secure. This gas library contains all AGA-compliant gas properties needed to make the algorithmic gas mass flow rate calculations.Flow Measurement Cost Savings
Both thermal and ultrasonic flow meters are preferred choices for flare gas measurement, but each has a different cost of ownership that should be understood. Let's briefly review costs and overall cost of ownership. Table 1 gives a five-year cost of ownership example comparing a traditional 6.0 inch (150 mm) long two-sensor insertion-probe thermal mass meter inserted into a 4.0 inch (100 mm) flare header, with an inline 4” (100mm) four-path inline ultrasonic meter, and a 6 inch (150 mm) long four-sensor insertion-probe thermal mass meter inserted into a 4” (100 mm) flare header. The upfront cost of a four-path ultrasonic meter averages $15,000 (Flow Research, Inc. 2008 Study), while the four-sensor thermal insertion-probe meter averages $3,000. Insertion-probe thermal meters also accommodate larger pipe applications up to 72 inches (2m) with a single 0.75 inch (19mm) insertion point. [caption id="attachment_4234" align="alignright" width="1024"]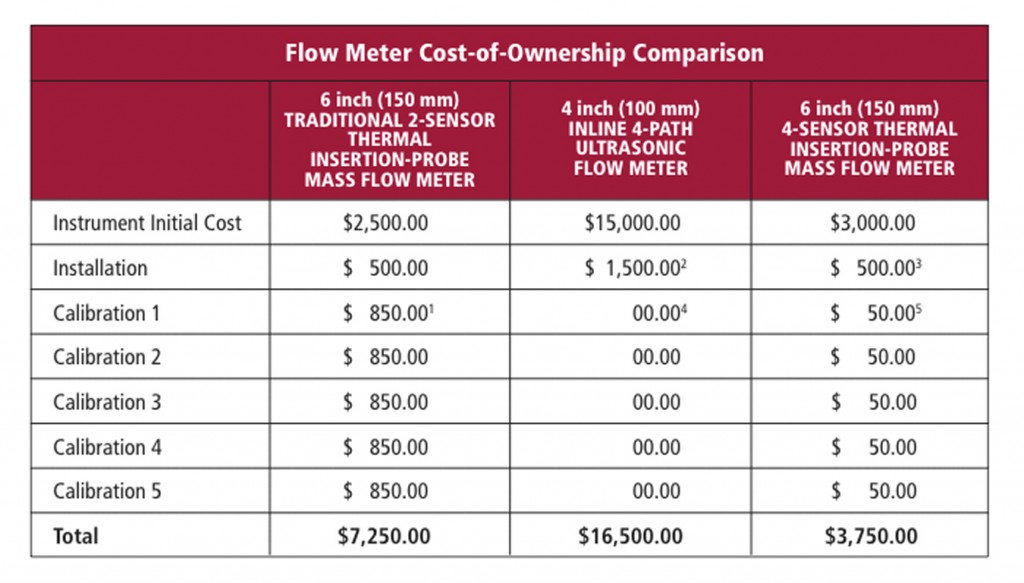