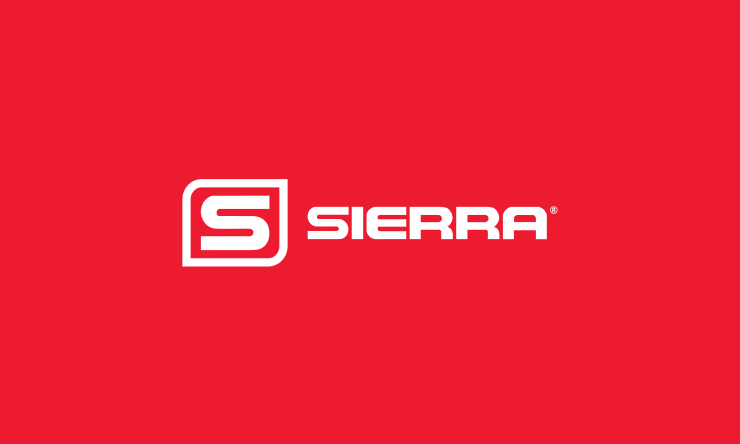
Natural Gas Measurement: 3 Reasons Thermal Mass Flow Meters Are Ideal
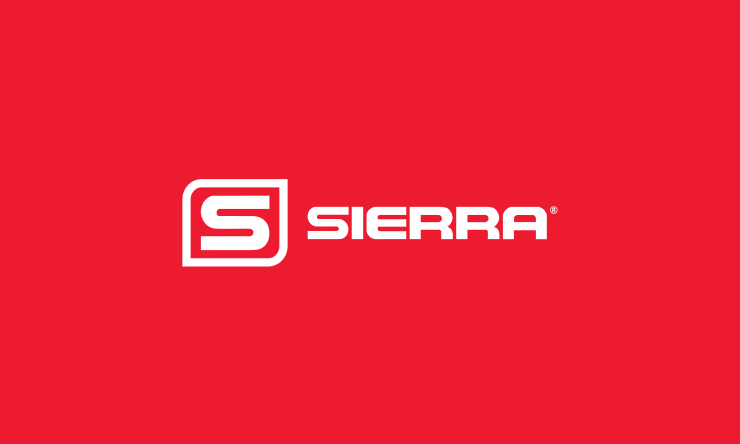
- No moving parts. As you can probably guess, moving parts can cause problems over time due to wear, lubrication and coating sensitivity. For example, turbine meters offer excellent accuracy, but they can easily be contaminated by dirt or rust, which is common in gas pipe lines. In addition, clearance for moving parts can result in slippage of the flow you're trying to measure. These issues can be avoided when you choose a thermal flow meter.
- Can accurately measure flow over large ranges. Thermal meters can measure almost to zero flow. This can be vital in determining leaks or small usages like pilot lights. More traditional meters (like bellows or turbines) need enough flow to start the wheels or blades rotating, while differential pressure devices (like orifice plates) need enough flow to cause a measurable pressure drop. Thermal meters require neither.
- Long life and high reliability. Sierra’s patented Dry-Sense® immersible thermal sensor has no moving parts, contains no epoxies or other compounds that will degrade over time and draws only a few milliamps of current. As such, Sierra warranties it for a lifetime of performance. Coupled with Sierra’s superior calibration technology and the ability to field-validate the meter, the Sierra Steel-Mass® 640S offers the most reliable solution for natural gas measurement.