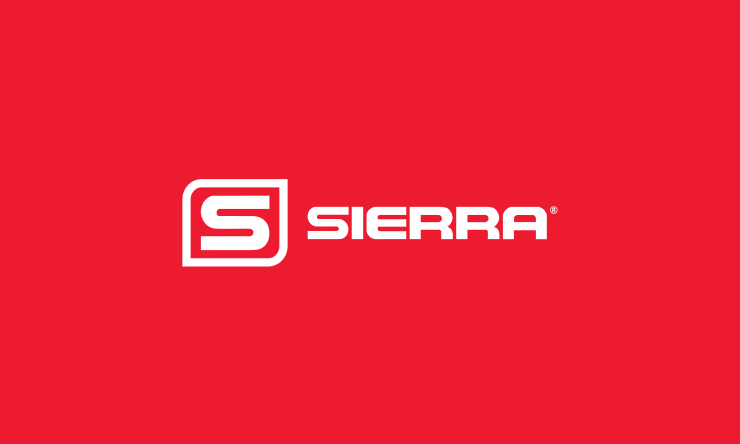
Not All Calibration Claims for Thermal Mass Flow Meters Are Equal
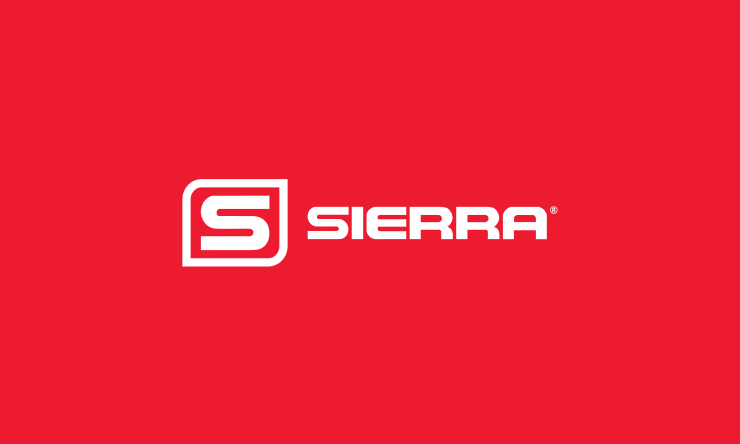
Editor’s Note: This post was originally published on September 4, 2014. Due to its popularity and continued questions on this issue, we updated the post on March 20, 2020.
It’s an industry fact that in-situ calibration validation is one of the major benefits of thermal mass flow meters. The idea of saving money and downtime by using in-situ” or “in place” flow meter calibration to assure flow meters are properly maintained and “in cal” to meet quality standards like ISO 9001 is an alluring idea for most engineers – especially those engineers for mid-to-large sized facilities and campuses where they have numerous devices. However, when evaluating thermal mass flow meters for in-situ calibration or validation capability, engineers should be aware that sensor drift will cause false positives that reduce the reliability of the validation.
Sensor Design – They Key to Accurate In-Situ Validation Calibration
Due to the inherent challenges of “wet” sensor design: shift & crack over time, unwanted sensor drift and gradual degradation of accuracy, Sierra’s founder Dr. John G. Olin invented Dry Sensor technology. Dry sensor technology is manufactured in a proprietary and highly controlled process to form such close contact that little or no air gap exists inside the sensor and no organic filler cements are needed.
Since its invention in 1999, the patented DrySense™ sensor has been the cornerstone sensor technology used on all Sierra thermal mass flow meters. The no-drift, all-metal, epoxy-free mechanical design provides the confidence that the in-situ calibration validation is actually valid. Most other sensors drift; therefore the claims of in-situ calibration simply are not accurate.
Discover more about why DrySensor sensor technology is essential for accurate in-situ calibration and learn about five methods and pitfalls of in-situ calibration validation you need to understand to assure your meter is running at optimal performance. Download white paper.